Continuous Annealing Furnace for Wire
LOI Thermprocess, with its predecessors Matthias Ludwig and Nassheuer, has been building Continuous roller hearth furnace plants under protective gas atmosphere for tubes, bars, wire coils and semi-finished annealing goods for more than 60 years. Throughout the world, more than 350 LOI roller hearth furnace plants under protective gas atmosphere have been installed.
Overview
Tenova LOI Thermprocess Continuous Annealing Furnace for Wire are used for heat treatment of tubes, bars, wire coils and semi-finished annealing goods.
Wire is annealed at temperatures up to 1,050 °C in roller hearth furnaces in a process gas atmosphere. The most important heat treatment procedures in roller hearth furnaces are the combination of bright annealing with
- stress relieving annealing
- recrystallization annealing
- normalizing
- tempering
- soft annealing
- solution annealing
- isothermal annealing.
Furnace atmosphere
Depending on the respective process requirements, LOI‘s roller hearth furnaces operate with defined protective gas and reaction gas atmospheres to avoid unwanted reactions such as the surface decarburization or the surface oxidation of the heat treated material. User-friendly and well-proven atmospheric control systems can help the plant operator e.g. to regulate the dew point or the carbon content in the reaction gas atmosphere.
Nitrogen is mainly used as carrier gas in the process gas. Hydrogen e.g. is added to it, which reduces, among other things, the oxide layers on the material surface and thus ensures achieving the blank annealing effect.
We apply a process technology particularly for the carbon-neutral annealing of steel that precisely regulates the proportion of carbon in the atmosphere by measuring the dew point. The so-called C-level control creates the optimal conditions for the heat treatment of the material surface. Under certain conditions, this technology is also applicable for carburizing annealing.
Depending on the process requirements or the local availability of the reaction gas – such as e.g. endogas, monogas, exogas or cracked ammonia – our experts optimize the process parameters with which the desired product properties are reliably achieved.
The roller hearth furnaces for wire distinguish themselves particularly with the vacuum and purging locks that are suitable for high coils. We use vacuum locks for materials with a considerable oxygen affinity. A purging lock is sufficient for materials that do not show a high affinity at the annealing temperatures in the furnace chamber. An intermediate part - the so-called "intermediate chamber" - is designed between the inner lock door and the access to the furnace chamber. This section protects the lock door from heat radiation from the furnace and thus increases the function and lifetime of this door.
Heating
It is possible to heat the furnaces both electrically and with fuel gas. As (one of the) first furnace manufacturer(s), LOI implemented gas and electric furnace heatings in the dual/hybrid system. In a dual heating system e.g., the heating up zones are equipped with burners, while the holding zones are electrically heated. Irrespective of the selected heating type, the precisely controlled temperature guidance is one of the essential quality characteristics of these furnaces.
The highly convective heat transfer ensures the rapid heating of the coils. Recirculation fans and guide plates guiding the heat flow ensure that the temperature is homogeneously distributed in the entire coil – even at low annealing temperatures.
In order to minimize the energy needs, we use heat exchangers to make waste heat usable again for the entire process, e.g. for drying or preheating the coils.
Cooling
Depending on the requirements, LOI applies different concepts in the cooling process. The cooling systems may feature low-temperature or high-temperature chambers as well as jet cooling; their design complies with the customers’ needs.
Moreover, the cooling systems can be equipped with heat recovery units and coupled with each other.
Process Guidance
Before the user-friendly in-house software transfers the appropriate annealing programs to the system, it first calculates them as function of the properties of the product to be treated as well as of the requested material features. Since the software controls the entire annealing process, it decreases the operator’s workload. In addition, the clearly structured, user-friendly furnace visualization system informs the operator at all times about the current state of both the process and the system components. The further data processing depends on the respective requirements; the actual data are either forwarded to a superordinate system, locally stored, or made available as a printout.
Optimizing the planned sequences and workflow, the software ensures a smooth, efficient process flow.
Resources
In order to minimize the energy needs and to save resources, we use efficient burners and heat recovery systems of our partners.
Heat exchangers make it possible to use the heat from the waste gas and/or cooling water at different temperature levels for e.g. heating pickling tanks, other production units or buildings. In this way, our customers optimally and efficiently use the energy flows.
Related Solutions
Europe
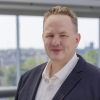
Erik Koenig
General Manager Sales Heat Treatment Plants - Atmosphere Furnaces, Tenova LOI Thermprocess
China
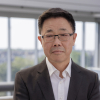
Peizhong Wang
Director of Sales Tenova LOI Thermprocess, Tenova Technologies (Tianjin)
Modernization, Service & Spare Parts
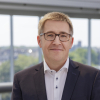
Marc Reynaert
Head of Revamp & Modernization, Tenova LOI Thermprocess