Hot Annealing and Pickling Line (H-APL) for Stainless Steel Strip
Tenova, with its over 40 years of experience, has the competence and knowledge of the thermal and chemical processes, terminal equipment mechanical design, control and automation know how which is required for the production of stainless steel strip.
Overview
The entry of an APL has a small sealing followed by a Preheating Furnace (PF). The strip is heated by waste gas coming from the Direct Fired Furnace (DFF), in the DFF strip is further heated to the required annealing temperatures and hold for certain soaking time. Strip is supported inside furnace by up-down rollers. After the annealing section, the strip enters a air cooling section followed by a water quench for final cooling and a wringer roller.
Descaling and Pickling are very important process in the manufacture of stainless steel, following the annealing operation and completing the transition between hot plant and cold plant.
The Descaling process remove the scale mechanically through eventual scale breaker and shot blasting and chemically (typically Sulfuric or Hydrochloric acid tanks) or through electrolytic descaling-pickling tanks.
The following pickling process is needed to dissolve a portion of the strip surface having not the correct percentage of alloy elements (so called Chromium depleted layer).
So generally the Descaling and Pickling processes involve a multi-step chemical reactions, and is one of the most polluting and costly chemical processes in the steel industry due to the presence of the highly corrosive acids and hazardous substances such as hexavalent chromium, nitrates and NOx.
Consequently in recent years Tenova has addressed its research activities to develop new pickling technologies aimed at reducing both the polluting effects of the chemicals used and the overall process operational costs.
Eco4 (ECOcological and ECOnomical stainless steel pickling process) is a new stainless steel pickling process developed by Tenova which avoids formation of hexavalent chromium (Cr6+) strongly improving the maintenance operator’s health and safety conditions, reduces electrical energy consumption (if a Tenova electrolytic tank is adopted), reduces or eliminate completely NOx and Nitrates in the waste water, reduces acid consumption.
The new process has not only a reduced environmental impact but also reduces the investment and operating costs for spent acid and waste waters regeneration and treatment.
Furthermore also fully re-generable acids solution is available, furtherly reducing or eliminating cost for waste treatment and sludge disposal, recovering acid ( as HCL or HF) and alloy metals (Cr, Ni, Mn.).
Related Solutions
Europe
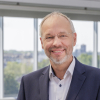
Wolfgang Eggert
General Manager Sales Heat Treatment of Steel Strip, Tenova LOI Thermprocess
China
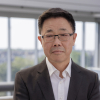
Peizhong Wang
Director of Sales Tenova LOI Thermprocess, Tenova Technologies (Tianjin)
Modernization, Service & Spare Parts
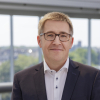
Marc Reynaert
Head of Revamp & Modernization, Tenova LOI Thermprocess